Underfill is used in the underfill process of Chip Scale Package (CSP) or
Ball Array Package (BGA). It can effectively reduce the overall temperature
expansion coefficient mismatch between the chip and the substrate or the impact
caused by external forces. Improve product durability and reduce the possibility
of failure.
Focus on performance:
reworkability
Underfill is often required to be reworkable. Since the value of the
printed circuit board (PCB) is high, if the chip is found to be defective, the
chip must be repaired. Reworkability allows the underfill to be removed for
reuse of the PCB, saving costs.
Youxingsha—Board-level underfill glue SHARK 1162 for the electronics
industry
Easy to repair as the
"core" wants
SHARK 1162 is a board-level underfill adhesive for the electronics industry
launched by Youxingshark. It is mainly used for filling BGA and CSP chip solder
joints. It is a one-component heat-cured epoxy adhesive and is a low-halogen
environmentally friendly product. This product has good filling properties,
reliability and reworkability, and has excellent performance in actual
industrial applications.
Features and
advantages
Low viscosity, good flow performance, low CTE, high Tg, low modulus, can be
repaired and cleaned
Technical
Parameters
Characteristics before
curing

Typical Cure
Properties
Recommended curing conditions: 10 min @ 130°C (can be adjusted
appropriately according to customer curing equipment and oven temperature)
Curing thermal weight loss: < 1%
Cured
properties

SHARK1162 is reworkable and easy to clean. After the colloid is heated to a
specific temperature and used with professional tools, it can be cleaned
efficiently without damaging the pad, improving the rework yield rate.
Product performance
display (3): repair operation
Due to the chemical properties of epoxy resin, SHARK 1162 exhibits glassy
properties after heat curing, with high body strength and bonding strength.
Improper repair can easily cause the pad to fall off, deform the PCB, or damage
the BGA. In order to better utilize the advantages of SHARK1162, this issue will
share the correct repair steps of SHARK1162.
Tools and materials
preparation
Tools: heat gun, soldering iron, rework bench, scraper
Materials: flux, soldering tape
1. At a distance of 2-3cm, use a hot air gun to evenly heat the chip and
its surroundings to 200-300°C.
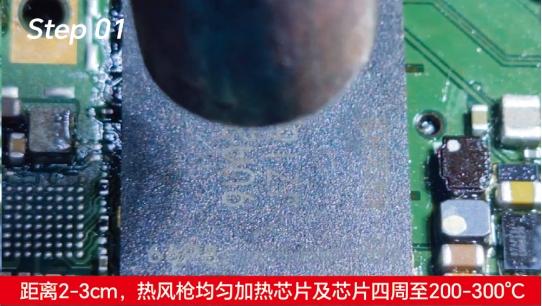
2. Use a blade to gently cut the glue joint between the chip and the bottom
of the board along the edge of the chip.
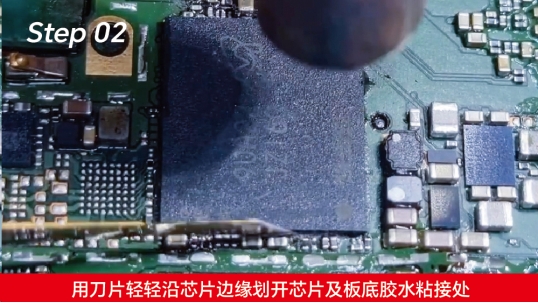
3. Apply flux to the edge of the chip, and continue to use the hot air gun
to evenly heat the entire chip.
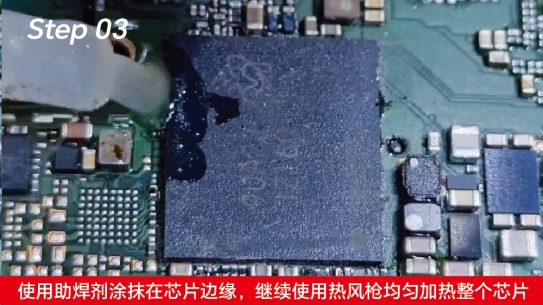
4. Use a scraper to gently insert one foot into the gap between the chip
and the bottom of the board, and try to lift the chip.
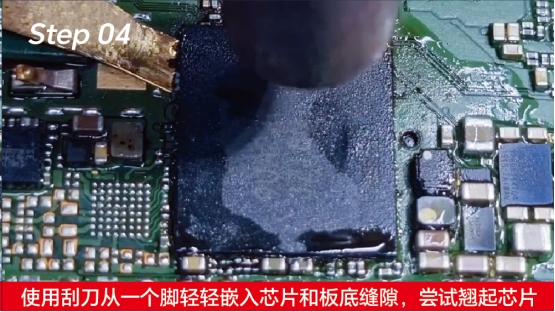
5. Cleaning the bottom of the board: Apply flux, use a hot air gun, and use
a scraper and a desoldering tape to carefully clean the residual glue and tin on
the board.
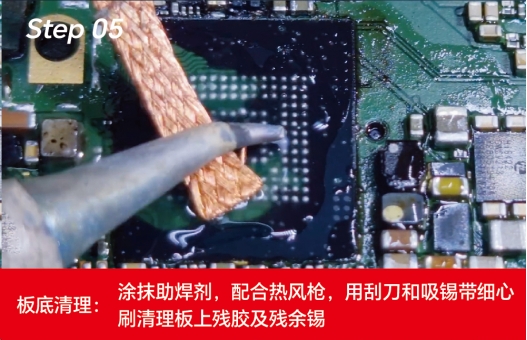
6. Chip cleaning: Apply flux and use a soldering tape and a soldering iron
to remove the residual solder paste on the chip. The recommended soldering iron
temperature is 230~280℃.
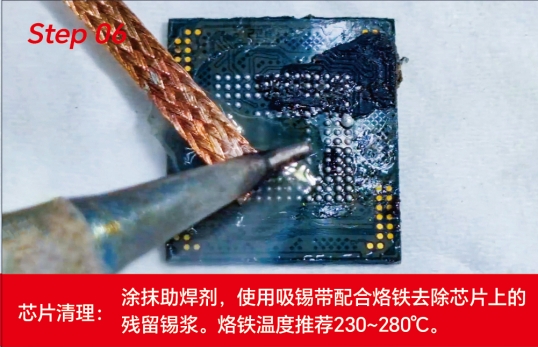
Precautions for
repair
1. Chip-level maintenance requires professionals
2. Heating temperature and maintenance time vary depending on chip size and
solder paste type.